When we think about transfusion safety, we usually focus on the testing, handling, and administration of blood products. However, it’s equally important to consider the containers used to transport these products to the patient.
To maintain product viability and ensure patient safety, blood and blood components must be kept within strict temperature ranges during transportation and storage. To achieve this, the Western Cape Blood Service (WCBS) delivers all blood and blood products in insulated hampers, often with ice bricks, to preserve their quality until the point of transfusion.
Because these hampers are costly, they are designed to be reused and must be returned to the blood bank after transfusion. Unfortunately, not all hampers are returned promptly, leading to shortages.
When hampers are unavailable, blood banks face operational delays. This may hinder their ability to issue blood products in a timely manner and, in urgent cases, forces them to use alternative containers that may not maintain optimal storage conditions. These challenges could directly impact the safety and effectiveness of the transfusion for patients.
Further compounding the issue, the redistribution of hampers between blood banks diverts vehicles that would otherwise be used to deliver specialised or urgent blood products.
To address this, WCBS is implementing a new system to track not only the blood products but also the blood hampers themselves. Each hamper will have a unique serial number and will be issued to specific wards. This will allow blood banks to trace where hampers are being delayed and investigate the root causes of shortages.
The first version of this hamper tracking system is currently under development and is expected to launch in April 2025.
Cooperation with regards to the timeous return of hampers will play a vital role in protecting blood product integrity and, ultimately, patient lives.
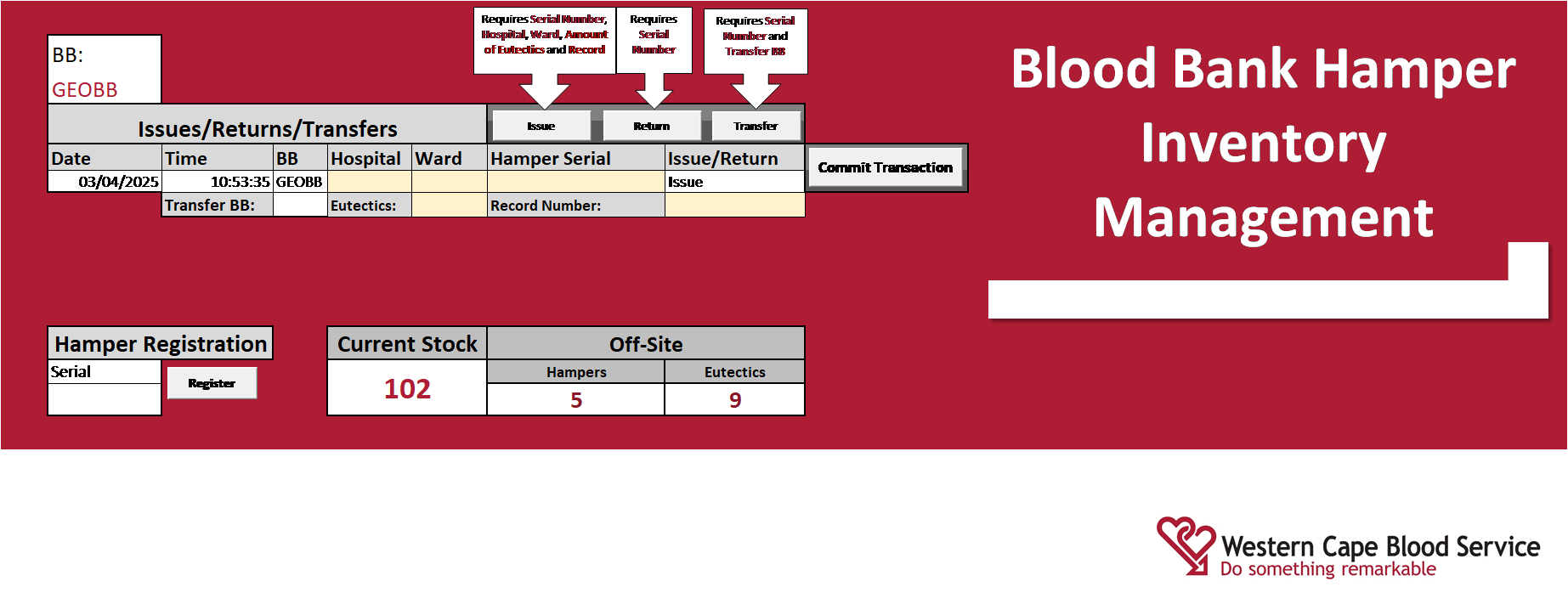
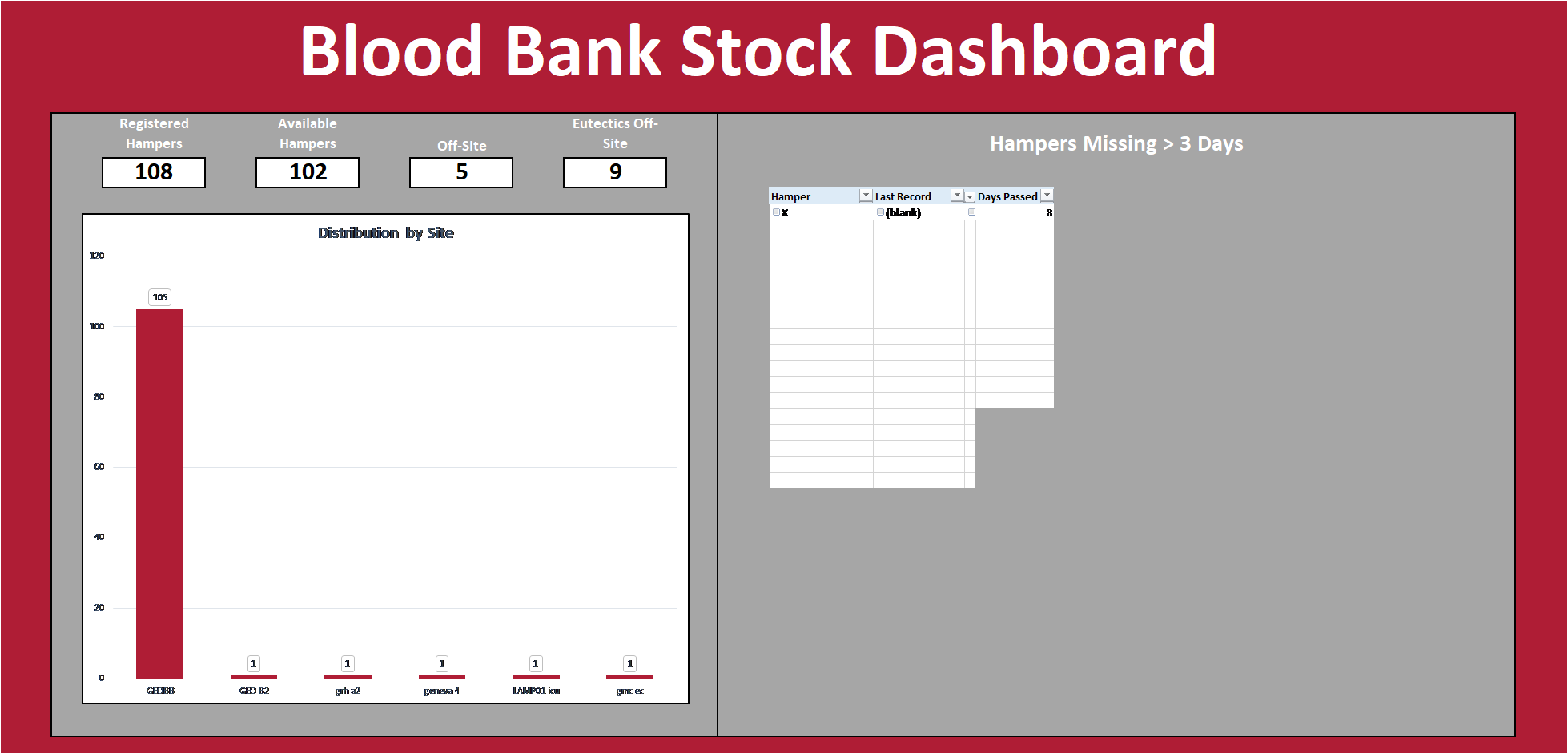
For more information about blood hampers, contact your closest blood bank.